
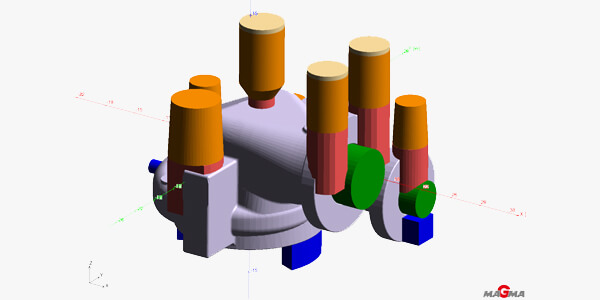
It can also quickly analyze various proposed design alternatives to make decisions such as whether a feature on a casting should be cast as part of the design or if it should be machined in later.
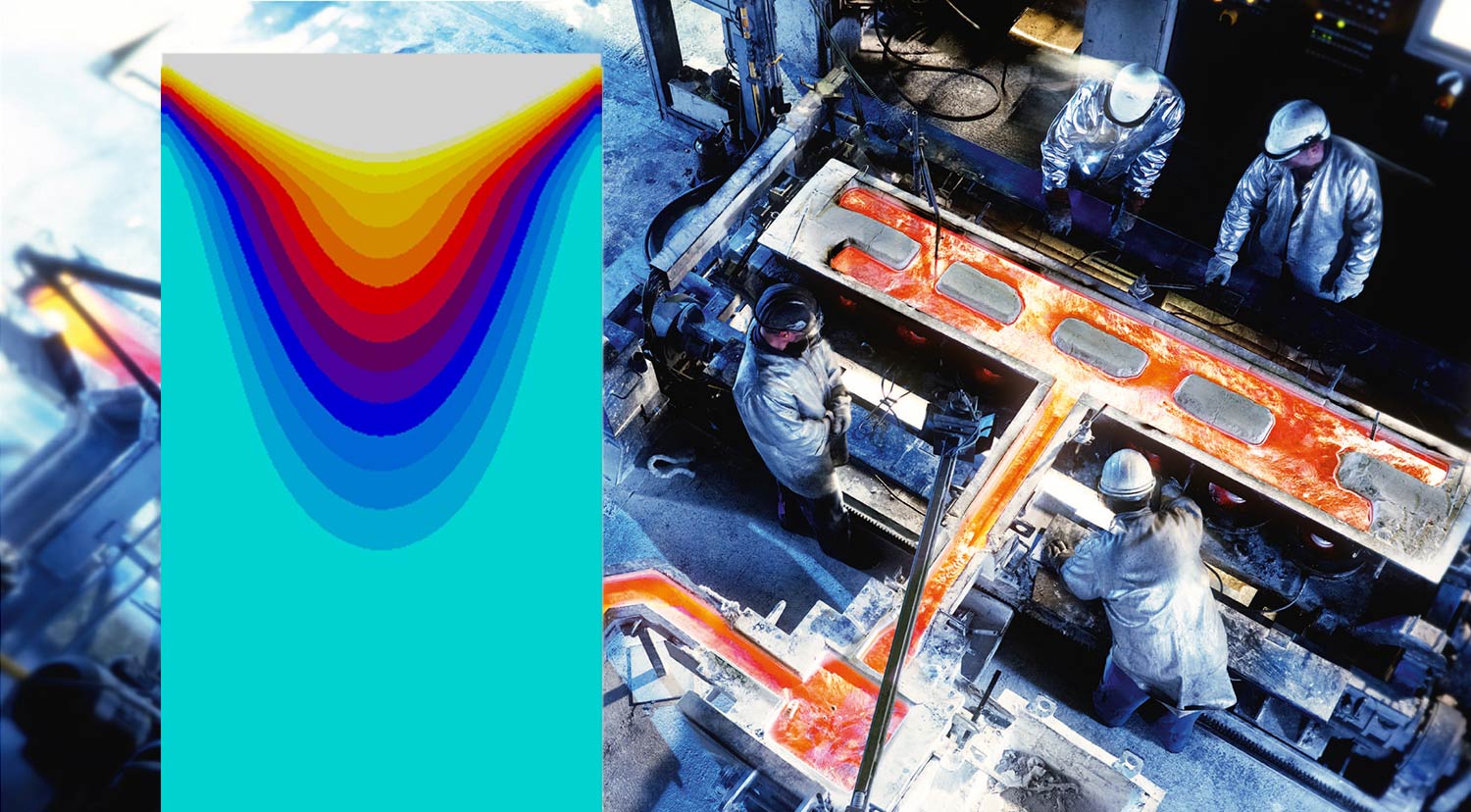
To name a few benefits of using MAGMASOFT’s casting process simulation enables leaps in innovation, as it allows for the consideration of the economic feasibility of proposed designs. By analyzing potential defects early in the design phase, the costs associated with eliminating these defects are also greatly reduced. Hence looking at the current scenario, MAGMASOFT has been on a mission to offer these MSMEs and SMEs to adopt best-in- standard technology and compete with the bigger players in the foundry industry.Ĭasting process simulation with MAGMASOFT aids in the casting design process by allowing designers to determine the manufacturability, final properties, and estimated costs associated with the production of a given casting design early in the design process. But however, 80-90 percent are MSMEs or Small and Medium Foundries. If we talk about India, it is the second largest foundry industry in the world when it comes to foundry production. MAGMASOFT has been catering to the players in the foundry industry, across the globe to seamlessly optimize casting processes By combining casting process knowledge with simulation competence, MAGMASOFT has been catering to the players in the foundry industry, across the globe to seamlessly optimize casting processes so as to bring in efficiency and productivity in operations. This Germany headquartered company incepted in 1988 has been on the forefront of evolution in casting process simulation with more than 30 years of industry experience. While we speak of robust and innovative casting solutions, without mentioning MAGMASOFT would be incomplete. Hence because of this, casting simulation has become an imperative industry standard in the foundry space to seamlessly carry out the entire process of casting with increased efficiency, accuracy, and productivity. Also, foundries relying on the traditional trial-and-error methods of the past to design casting processes are finding it more and more challenging to compete, due to the lack of quick response capabilities to customer requirements, inaccuracy and long lead times. As per a credible report, nearly 90 percent of the defects in components are due to mistakes in design where the costs to change the design can be unimaginable.
